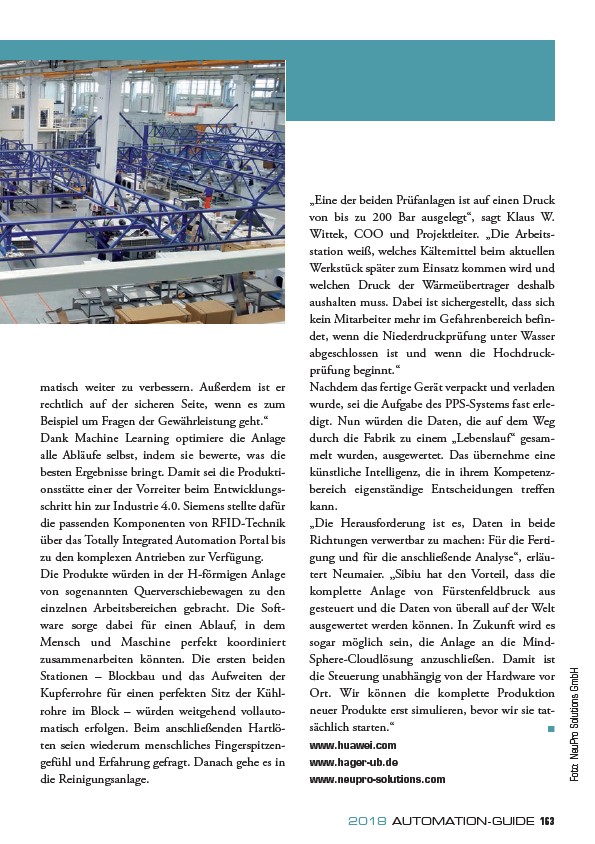
2018 AUTOMATION-GUIDE 163
matisch weiter zu verbessern. Außerdem ist er
rechtlich auf der sicheren Seite, wenn es zum
Beispiel um Fragen der Gewährleistung geht.“
Dank Machine Learning optimiere die Anlage
alle Abläufe selbst, indem sie bewerte, was die
besten Ergebnisse bringt. Damit sei die Produktionsstätte
einer der Vorreiter beim Entwicklungsschritt
hin zur Industrie 4.0. Siemens stellte dafür
die passenden Komponenten von RFID-Technik
über das Totally Integrated Automation Portal bis
zu den komplexen Antrieben zur Verfügung.
Die Produkte würden in der H-förmigen Anlage
von sogenannten Querverschiebewagen zu den
einzelnen Arbeitsbereichen gebracht. Die Software
sorge dabei für einen Ablauf, in dem
Mensch und Maschine perfekt koordiniert
zusammenarbeiten könnten. Die ersten beiden
Stationen – Blockbau und das Aufweiten der
Kupferrohre für einen perfekten Sitz der Kühlrohre
im Block – würden weitgehend vollautomatisch
erfolgen. Beim anschließenden Hartlöten
seien wiederum menschliches Fingerspitzengefühl
und Erfahrung gefragt. Danach gehe es in
die Reinigungsanlage.
„Eine der beiden Prüfanlagen ist auf einen Druck
von bis zu 200 Bar ausgelegt“, sagt Klaus W.
Wittek, COO und Projektleiter. „Die Arbeitsstation
weiß, welches Kältemittel beim aktuellen
Werkstück später zum Einsatz kommen wird und
welchen Druck der Wärmeübertrager deshalb
aushalten muss. Dabei ist sichergestellt, dass sich
kein Mitarbeiter mehr im Gefahrenbereich befindet,
wenn die Niederdruckprüfung unter Wasser
abgeschlossen ist und wenn die Hochdruckprüfung
beginnt.“
Nachdem das fertige Gerät verpackt und verladen
wurde, sei die Aufgabe des PPS-Systems fast erledigt.
Nun würden die Daten, die auf dem Weg
durch die Fabrik zu einem „Lebenslauf“ gesammelt
wurden, ausgewertet. Das übernehme eine
künstliche Intelligenz, die in ihrem Kompetenzbereich
eigenständige Entscheidungen treffen
kann.
„Die Herausforderung ist es, Daten in beide
Richtungen verwertbar zu machen: Für die Fertigung
und für die anschließende Analyse“, erläutert
Neumaier. „Sibiu hat den Vorteil, dass die
komplette Anlage von Fürstenfeldbruck aus
gesteuert und die Daten von überall auf der Welt
ausgewertet werden können. In Zukunft wird es
sogar möglich sein, die Anlage an die Mind-
Sphere-Cloudlösung anzuschließen. Damit ist
die Steuerung unabhängig von der Hardware vor
Ort. Wir können die komplette Produktion
neuer Produkte erst simulieren, bevor wir sie tatsächlich
starten.“
www.huawei.com
www.hager-ub.de
www.neupro-solutions.com
Foto: NeuPro Solutions GmbH